Quels sont les avantages et les défis liés à l’adoption des principes Just in Time (JIT) dans une Supply Chain mondiale ? Comment peut-on faire pour relever ces défis?
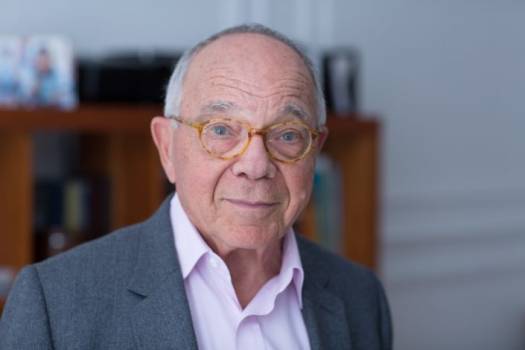
Je ne connais aucune Supply Chain travaillant sur un principe de Juste à Temps, c’est-à-dire sur des opérations synchronisées à tous les niveaux de la chaîne d’approvisionnement à une échelle régionale ou mondiale. Juste à temps. Le produit sort d’une phase de production et passe immédiatement dans la phase suivante. Il s’agit de synchronisation totale. On a transformé le stock statique en flux. C’est ce que l’on trouve sur des lignes de conditionnement par exemple. Dans les brasseries, une ligne d’embouteillage peut produire 100.000 bouteilles par heure, palettisées et expédiées. Même chose avec le pet food. Pourtant dans beaucoup d’usines, la synchronisation apparaît plus difficile. Très souvent, le temps de cycle (délai entre la mise en production et la sortie du produit fini) prendra 100 fois la somme des temps de production (temps pendant lequel une transformation du produit a lieu). Par exemple on mettra 3 mois pour sortir un flacon de parfum décoré alors qu’il ne faut que quelques minutes de temps opératoire, le temps effectif pendant lequel une transformation se produit.
Le projet Onde Verte
Pour relever le défi, nous avons mis au point une méthode dite Onde Verte ou mise en ligne virtuelle. Cela revient à faire dessiner à priori une ligne de production virtuelle, transversale à travers tous les ateliers nécessaires pour la production. On a remplacé des chefs d’atelier par des conducteurs de ligne virtuelle. Ces lignes ne sont montées que pour quelques heures par semaine ou mois. Cette méthode permet de faire passer la durée du cycle de fabrication (délai entre lancement en production et sortie du produit fini) de quelques mois à quelques heures. Elle peut être utilisée dans tous les procédés de production où on découple les opérations. Très souvent par exemple on trouve des procédés où on commence par fabriquer un « jus » que l’on va ensuite conditionner. Au lieu de découpler ces opérations via des cuves de stockage on va les synchroniser. Cela permet d’éviter les fonds de cuve et donc de réduire le nombre de cuves et . C’est l’exact inverse du DDMRP. Au lieu de découpler les opérations en introduisant des stocks locaux on ordonnance les opérations à priori. Dans l’industrie textile on peut ainsi construire des lignes de production virtuelles entre plusieurs usines. La méthode est très puissante. Et elle peut être utilisée pour synchroniser les fournisseurs avec les clients. L’idée à la base est la même que celle de la coordination des feux de circulation dans une avenue à sens unique pour que véhicules roulant à 50km/h ne soient pas arrêtés à un feu rouge. Dans une suite d’ateliers, on imposera une cadence de circulation par famille technique de produits.
Cette méthode permet de réduire drastiquement les délais. Elle a un autre gros avantage. Elle simplifie grandement la planification de production. Son inconvénient peut-être est qu’elle requière des prévisions de la demande future à minima et maxima par famille de produits. Mais quel type de supply chain agile n’en requière pas de nos jours?
Jean-Patrice Netter
Président de DIAGMA
Pour lire d’autres articles de Jean-Patrice Netter :