Le DDMRP, ce n’est pas du MRP (Material Requirements Planning), et ce n’est pas vraiment Demand Driven (DD). C’est une méthode qui met en place des stocks le long de la Supply Chain. Un peu comme on mettrait en place des écluses pour réguler le cours d’une rivière. Ces stocks déclenchent au jour le jour …
Continuer à lire « DDMRP : DU VOL A VUE POUR PILOTER LES FLUX »
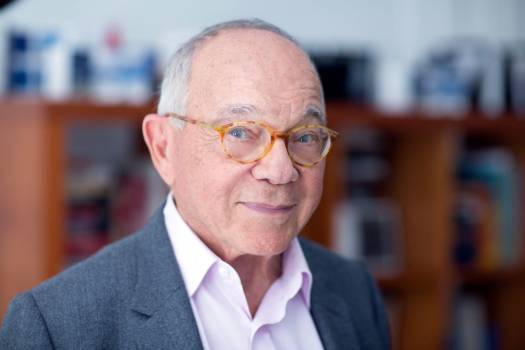
Le DDMRP, ce n’est pas du MRP (Material Requirements Planning), et ce n’est pas vraiment Demand Driven (DD). C’est une méthode qui met en place des stocks le long de la Supply Chain. Un peu comme on mettrait en place des écluses pour réguler le cours d’une rivière.
Ces stocks déclenchent au jour le jour leur approvisionnement sur seuil d‘alerte. C’est du Kanban amélioré.
Le DDMRP n’est pas du MRP parce que justement ce n’est pas du planning. C’est local, pas global. C’est décentralisé.
Le DDMRP n’est pas Demand Driven ou alors « demand driven » par ricochet. C’est un système opérationnel de la famille du Kanban. Chaque stock se pilote en fonction de la demande qu’il ressent.
Un seuil d’alerte pour chaque stock
C’est une méthode de pilotage individualisé de chaque stock de la supply chain. Chaque stock fonctionne sur seuil d’alerte. Ce seuil d’alerte, comme dans toute gestion des stocks, est une estimation de la demande maximale pendant le délai maximum supposé d’approvisionnement. Cette estimation est simple dans le DDMRP. Elle s’appuie sur la moyenne des quelques demandes passées. Le DDMRP est court-termiste. Il faut l’accompagner par des prévisions et de la planification.
Comment ça fonctionne
Cela fonctionne de la manière suivante. Imaginez un ensemble de pièces qui une fois assemblées donnera une roue. Vous décidez d’avoir un stock de roues plutôt que des roues qui partent vers l’étape suivante d’assemblage. Et supposons qu’il vous faut 3 jours en moyenne pour obtenir les pièces et les monter pour obtenir une roue. Tant que le stock de roues reste au-dessus d’un seuil d’alerte, qui est égal à 3 jours de demande maximale « estimée », tout va bien. Vous êtes dans le vert. L’approvisionneur est rassuré. Il ne bouge pas. Si le stock descend en dessous du seuil d’alerte, feu orange, danger, il passe une commande d’approvisionnement à ses fournisseurs de pièces pour ne pas tomber dans le rouge. Dans le rouge rien ne va plus. Vert, orange, rouge. Le drapeau de l’Éthiopie.
Le DDMRP fonctionne si…
…l’environnement est stable et n’est pas trop contraint. Si la demande est épisodique le système fera du « un pour un », c’est-à-dire qu’il renouvellera ce qui vient de partir. Très utile par exemple pour des rouges à lèvres dont le nombre de teintes est très grand et certaines teintes à ventes très épisodiques. Si la demande varie beaucoup à la hausse ou à la baisse, le système tente de rattraper en augmentant ou en baissant le niveau du stock local. C’est un jeu de poursuite.
Mais le DDMRP pose problème…
dans un environnement complexe, proche de la saturation, avec des contraintes transversales, lorsqu’on ne sait pas estimer le délai d’approvisionnement d’un stock parce qu’il dépend de la charge du reste du réseau. Pour pouvoir estimer ce délai il faut planifier l’ensemble. Il faut voir « the big picture ».
Un manque de coordination
Le DDMRP c’est un peu comme si, pour piloter, on mettait un petit moteur dans chaque roue d’une voiture. Chaque moteur est indépendant, répondant aux informations locales qu’il reçoit. Ce peut être par exemple la vitesse de la roue sur la chaussée. Selon sa vitesse d’avancement sur la chaussée, chaque roue et donc chaque moteur s’ajuste pour rester à la même vitesse. En côte la roue doit accélérer pour maintenir la vitesse, en descente ralentir. Dans un virage, c’est plus compliqué parce qu’il n’y a aucune coordination entre les roues. La roue extérieure au virage accélère, le moteur va la ralentir, la roue intérieure au contraire va ralentir, le moteur va l’accélérer. La voiture va déraper et faire un tête-à-queue. Il n’y a pas de coordination entre roues.
C’est le risque du DDMRP. Le système peut s’emballer. Il n’y a aucune coordination globale entre stocks. En régime stable tout va bien. S’il y a des contraintes de production, une saisonnalité, des promotions, des articles à ventes épisodiques, des contraintes de capacité, des conditions de vente, des paramètres de production… patatras, rien ne va plus !
Chacun pour soi
Avec le modèle de base du DDMRP, on ne peut pas gérer conjointement plusieurs produits. De même si les Supply Chain sont longues et que la demande varie tout d’un coup (promotion, influenceur, black Friday…), on ne sera prévenu en amont que très tard alors qu’on aurait pu anticiper la demande. Et plus on augmente le nombre de stocks à gérer, plus le système génère de stock. Le découplage c’est bien, cela apaise le système, mais cela génère beaucoup de stock. Avec beaucoup de stock à chaque niveau (des amortisseurs), la Supply Chain n’a aucun problème. Sauf évidemment si elle doit gérer des produits frais. Ou si elle veut gérer efficacement.
Planifier avant de tirer le flux
Le fonctionnement d’une Supply Chain n’est pas toujours assez simple pour que le DDMRP puisse fonctionner correctement. S’il y a des contraintes un peu globales qui relient plusieurs stocks, il faudrait commencer par planifier les capacités pour calculer les délais maxima d’obtention de chaque article semi-fini à partir de ses fournisseurs internes ou externes. Ceci permettrait de paramétrer le DDMRP sinon le système ne peut fonctionner de manière cohérente.
Le DDMRP est un complément de la planification
Il a pour vocation de réguler les flux au jour le jour dans la Supply Chain. Ce n’est ni un outil stratégique (S&OP), ni même tactique (plan hebdomadaire ou ordonnancement). C’est un outil opérationnel qui a l’immense mérite, grâce au marketing omniprésent qui l’accompagne, de susciter un réexamen des paramètres de gestion des flux dans des entreprises qui ont du mal à les maîtriser.
Certes il manque de vision globale. Pour le faire fonctionner, il faut commencer par planifier les capacités, mettre en place les ressources adéquates, s’assurer qu’il y a une solution réalisable qui respecte les contraintes à moindre coût. Ensuite, et seulement ensuite, on pourra mettre en place un DDMRP, si l’on a choisi cette méthode, pour approvisionner quotidiennement les stocks que l’on a choisi de réguler.
Jean-Patrice Netter
Président de DIAGMA
Autre article sur le DDMRP