DDMRP : driving the supply chain from the bottom up Jean-Patrice Netter, President of Diagma DDMRP is not MRP (Materials Requirement Planning), and it is not really Demand Driven (DD). It is a method that sets up stocks along the Supply Chain. Each stock places orders to the stock upwards on the flow. A bit …
Continue reading “DDMRP: driving the supply chain from the bottom, up”
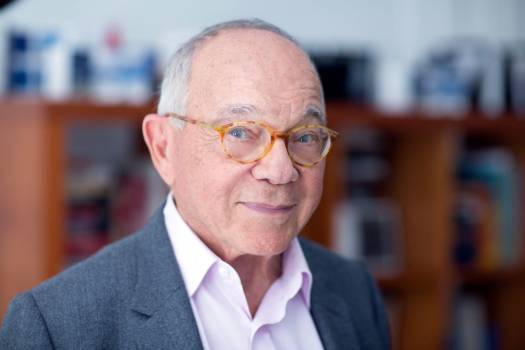
DDMRP : driving the supply chain from the bottom up
Jean-Patrice Netter, President of Diagma
DDMRP is not MRP (Materials Requirement Planning), and it is not really Demand Driven (DD). It is a method that sets up stocks along the Supply Chain. Each stock places orders to the stock upwards on the flow. A bit like setting up locks to regulate the course of a river.
These stocks trigger a replenishment when the stock level reaches an alert threshold. It’s improved Kanban.
The DDMRP is not MRP because there is no planning. It’s local, not global. It’s decentralized.
The DDMRP is not Demand Driven or if so, “demand driven” by ricochet. It’s an operational system of the Kanban family. It manages local inventory from the demand it senses locally.
An alert threshold for each STOCK
It is a method of individualized management of each stock of the supply chain. Each stock runs on an alert threshold. This alert threshold, as with many inventory management systems, is an estimate of the maximum demand during estimated maximum supply lead time. This estimate is simple in the DDMRP. It is based on the average of the few past requests. It is short-sighted. The future is a few steps behind, in the past.
HOW IT WORKS
It works in the following way. Imagine a set of components that once assembled will become a wheel. You decide to have a stock of wheels rather than wheels that go directly to the next assembly stage. And suppose it takes you 3 days on average to get the parts and mount them to get a wheel. As long as the stock of wheels stays above the recent average demand for 3 days, plus a “certain percentage” as a safety, all is well. You’re in the green. The replenisher is reassured. He’s stays put. If the stock drops below some safety level (the threshold), orange light, danger, place a supply order to this part supplier so as not to fall into the red. In the red nothing goes any more. Green, orange, red.
The DDMRP WORKS IF…
… the environment is stable and not too constrained. It is a variant of kanban, on a large scale. If the demand is episodic, the system will replenish “one for one”, that is, it will renew what has just been consumed. Very useful for example for lipsticks with a very large number of shades and some shades with very episodic sales. While demand varies greatly upwards or downwards, the system tries to catch up by increasing or lowering the level of the local stock. It’s a chase game.
BUT it will fail…
in a complex, close to saturation environment, with transverse constraints where it is not known how to estimate the time to supply a stock because it depends on the load of the rest of the network. In order to estimate this lead time, it is necessary to plan the whole. You have to see “the big picture.”
LACK OF COORDINATION
The DDMRP is a bit like driving with a small engine in every wheel of a car. Each engine is independent, responding to the local information it receives. This can be for example the speed of the wheel on the pavement. Depending on its speed of progress on the roadway, each wheel and therefore each engine adjusts to stay at the same speed. Climbing a hill, the wheel must accelerate to maintain the speed, descending slow down. In a turn, it becomes more complicated because there is no coordination between the wheels. The wheel outside the turn accelerates by itself, the engine will slow it down, while the inner wheel will slow down by itself and its engine will accelerate it. The car’s going to skid and go head-to-head. There is no coordination between wheels.
This is the risk of DDMRP. The system can get carried away. There is no overall coordination between stocks. In a stable regime everything is fine. If there are production constraints, seasonality, promotions, episodic sales items, capacity constraints, sales conditions, production parameters… wham, nothing goes!
EVERYONE FOR himself
With the DDMRP model one cannot jointly manage several products. Similarly, if the supply chain is long and the demand varies all of a sudden (promotion, influencer, black Friday…), we will not be notified beforehand until very late when we could have anticipated the demand. And the more stocks you manage, the more stock the system generates. Decoupling is good, it soothes the system but it generates a lot of stock. With a lot of stock at each level (shock absorbers) the supply chain has no problem. Unless, of course, it has to handle fresh produce. Or if it wants to manage effectively.
PLAN BEFORE YOU PULL THE FLOW
The operation of a supply chain is not always simple enough for the DDMRP to function properly. If there are somewhat global constraints that link multiple stocks, the first step would be to plan capacity to compute the maximum time frames for obtaining each semi-finished item from its internal or external suppliers. This would set up the DDMRP otherwise the system cannot function consistently...
The DDMRP COMPLEMENTs planning
Its purpose is to regulate flows in the supply chain. It is neither a strategic tool (S&OP), nor tactical (production planning or scheduling). It is an operational tool that has the immense merit, thanks to the ubiquitous marketing that accompanies it, to prompt a review of the parameters of flow management in companies that have difficulty mastering them.
Certainly, it lacks a global vision. To make it work, you have to start by planning capacity, putting in place the right resources, making sure that there is a workable solution that meets the constraints at a lower cost. Then, and only then, can you set up a DDMRP, if you have chosen this method, to supply the stocks that you have chosen to regulate.