Transform the disadvantage of “poor forecasts” into an opportunity to improve them and optimize your entire Supply Chain by following the Diagma view described below.
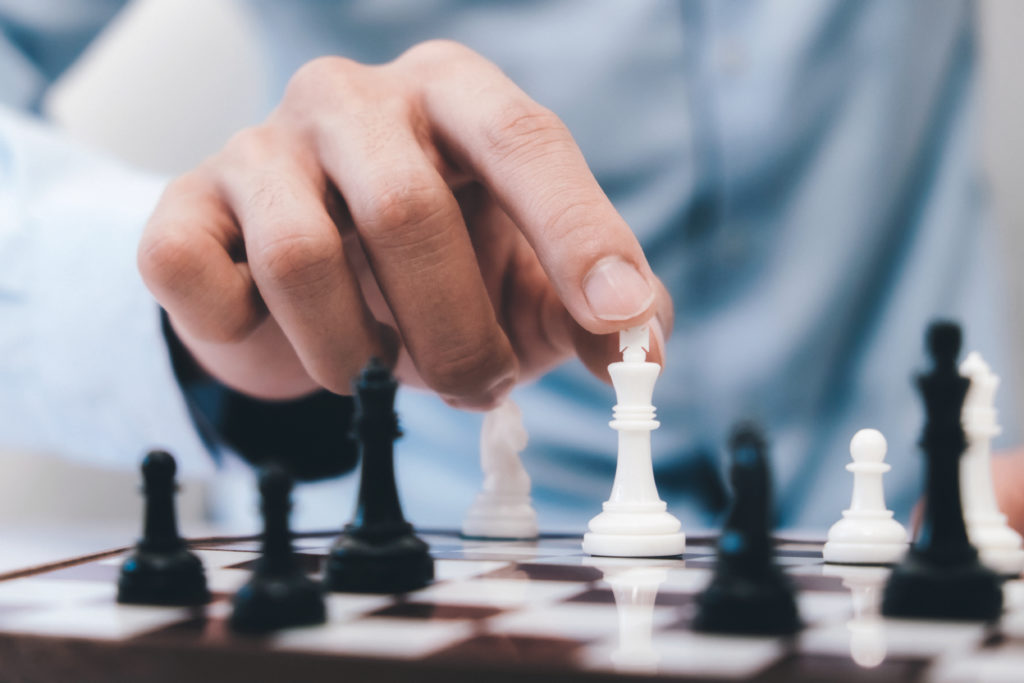
Take advantage of “poor quality” forecasts
To gain a competitive advantage and ensure the success of your business, you must continuously improve your Supply Chains. This means constantly finding the optimal compromise to provide good quality products, with good service levels, at minimal cost. But what if demand forecasting issues creep into your planning processes and degrade your service and costs?
A 3-step process to improve your forecasts and procurement
Diagma’s approach makes it possible to rectify any forecast of demand (regardless ofthe method to obtain it), to remove the bias and estimate its maximum error. Indeed, there will always be uncertainty in your forecasts. Too many companies worry about this uncertainty without calculating it and exploiting it fully to their advantage. Instead of trying to “guess right” with their forecasts, we recommend that companies follow these steps:
1st mistake: you think you need a safety stock in number of days of sale, you think that safety stock must be a percentage of the forecast
In reality, if you compare your forecasts with with actual demand, you will find that this is not the case. In general, the error is rather an absolute value. For example, you are wrong by a maximum of 500 units in your forecast whether your forecast is 2000 in off-peak periods or 5000 in peak periods.
2nd mistake: your forecasts are biased, always too optimistic or pessimistic
Visualize the quality of your forecast on a chart with the forecast on the abscissa and the actual ordered as the ordinate. If you were a soothsayer all the points would be on the first bisector. This is probably not the case. If you find many more points below the bisector or many more above, this is a good indicator that your forecast is probably biased. If this is the case, draw the regression line that passes through the points. The equation of this line gives you a better forecast. It is no longer biased and the gap between your points and this new line allows you to measure the forecast error. For example, most of your points are less than 500 above the line. So your maximum demand will be 500 above the forecast.
3rd mistake: You use the forecast to replenish your stock or plan production
The forecast is only an average. Using it gives you a one in two chance of stockout. Except if you use the so called safety stocks, often miscalculated. Drop these safety stocks and plan from the maximum expected demand. Instead of safety stock you may decide for example to have manpower on offer if demand requires.
Use the maximum expected demand to feed into your planning processes. This will allow you to optimize your flows. And to make the best use of your resources, reduce your stocks. You will get better customer service. You will reduce your costs.
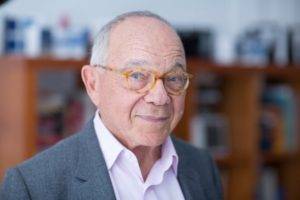
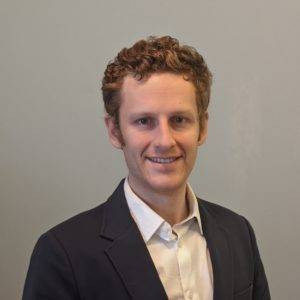
To download white paper, click here!
Articles from same author :
What is the difference between supply chain, operations, and logistics?
Hashgraph, the future of the Blockchain for Complex Supply Chains