On commet 4 erreurs qui peuvent conduire à des ruptures dans la Supply Chain, quand on gère une chaîne d’approvisionnement : Sous-estimer le délai d’approvisionnement maximum Sous-estimer la demande maximum Surestimer le coût du stock Oublier que le stock n’est pas la seule solution pour ne pas avoir de ruptures. Prenons ces points susceptibles d’occasionner …
Continuer à lire « EVITEZ LES RUPTURES DANS VOTRE SUPPLY CHAIN »
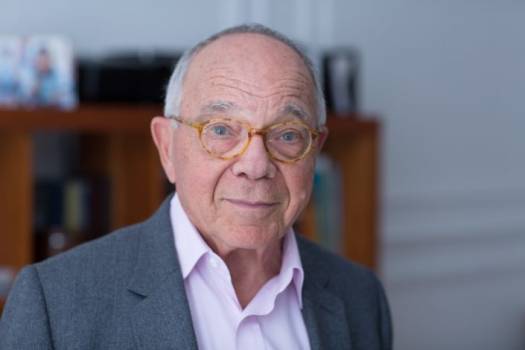
On commet 4 erreurs qui peuvent conduire à des ruptures dans la Supply Chain, quand on gère une chaîne d’approvisionnement :
- Sous-estimer le délai d’approvisionnement maximum
- Sous-estimer la demande maximum
- Surestimer le coût du stock
- Oublier que le stock n’est pas la seule solution pour ne pas avoir de ruptures.
Prenons ces points susceptibles d’occasionner des ruptures dans la Supply Chain un par un :
1. Pour le délai d’approvisionnement maximum,
Vous pouvez évidemment avoir plusieurs sources d’approvisionnement avec des délais et des coûts différents. Par contre, pour chacune de ces sources, il faut bien enregistrer leurs performances à partir d’un historique de leurs livraisons. Il faut aussi tenir compte des délais des différentes opérations entre le moment où leur produit est disponible et leur arrivée sur notre site (documentation , transport par type, douane …). L’analyse des délais observés doit de plus nous indiquer s’il y a une tendance à l’augmentation ou à la diminution, s’il y a une saisonnalité … C’est une démarche d’analyse et de prévision. Au total le délai observé peut être prévu et suit une loi de probabilité empirique (pas nécessairement Gauss ou Poisson ou …) qui nous dit qu’avec un certain pourcentage de certitude (99.9% par exemple) le délai n’excédera pas un laps de temps donné. Appelons le Lmax (lead-time maximum).
2. Pour la demande maximum,
pendant le délai précédemment choisi (Lmax), la démarche est semblable : analyser les données, prévoir et calculer la demande maximum. Il faut pour cela constituer un historique de la demande pendant le délai d’approvisionnement maximum. Si la demande pour le produit est épisodique et que l’on ne s’attend pas à ce que ce produit devienne un best seller, il suffit de prendre le maximum observé, s’il n’est pas trop atypique. Pour les autres, il faut faire des prévisions et calculer le maximum possible.
3. Pour le coût du stock,
il faut bien voir qu’il est constitué de 2 parties. L’un tient à la nature physique du stock, l’autre à son constituant financier.
- Pour ce qui est du physique, si vous stockez dans un entrepôt dont vous êtes propriétaire, en gros l’emplacement de stockage, s’il en reste, ne vous coûte rien.
- Pour ce qui est du financier, il comporte 2 aspects :
- à quel taux vous êtes capable d’emprunter pour financer un stock (en général pour un organisme financier c’est un prêt peu risqué (avec des taux de moins de 1% début 2020)
- le risque d’obsolescence. Pour cela, il faut analyser les bilans pour observer les provisions pour risque d’obsolescence au fil des années. En pourcentage de la valeur du stock, il vous donnera le taux à ajouter au taux d’emprunt pour financer le stock. Ce taux peut alors atteindre 10%, si le stock est mal géré.
4. Enfin, et il faut le souligner, le stock n’est pas la seule solution pour éviter les ruptures dans la Supply Chain.
Pour illustrer ce point, voici une petite anecdote. Un jour le directeur des opérations d’un très gros brasseur pour lequel nous travaillions depuis longtemps m’a demandé s’il serait possible d’étudier une alternative à la constitution d’un stock d’avant saison pour ses brasseries. L’habitude en effet était de produire « plein pot » de début Janvier jusqu’à Juin pour constituer ce stock. En France, en particulier, on consomme plus de bière en été que pendant les autres saisons. Le problème est cependant qu’on ne sait jamais quand la saison va s’arrêter, et que l’on reste avec beaucoup trop de stock en fin de saison. Or la bière est un produit périssable. Au bout de 3 mois, son goût se modifie subtilement. Nous avons donc étudié une solution de constitution d’un stock inférieur au besoin maximum envisagé mais qui pouvait être complétée par une production les week-ends en maintenant le personnel en astreinte, c’est-à-dire chez eux, avec un risque d’être appelé en production en cas de surchauffe. Cela a permis de diviser le stock par 2 et de supprimer le stock obsolète.
Pour lire d’autres articles de Jean-Patrice Netter,