To increase the performance of your warehouse, the quality of preparation of its orders or reduce the difficulty of your operators, automating can seem attractive. But beware of the many pitfalls that await you. Being accompanied by experts who have already carried out several automation projects makes it possible to defeat them and achieve realistic objectives. This is what advocates François Rochet, Partner of DIAGMA, experienced in the exercise …
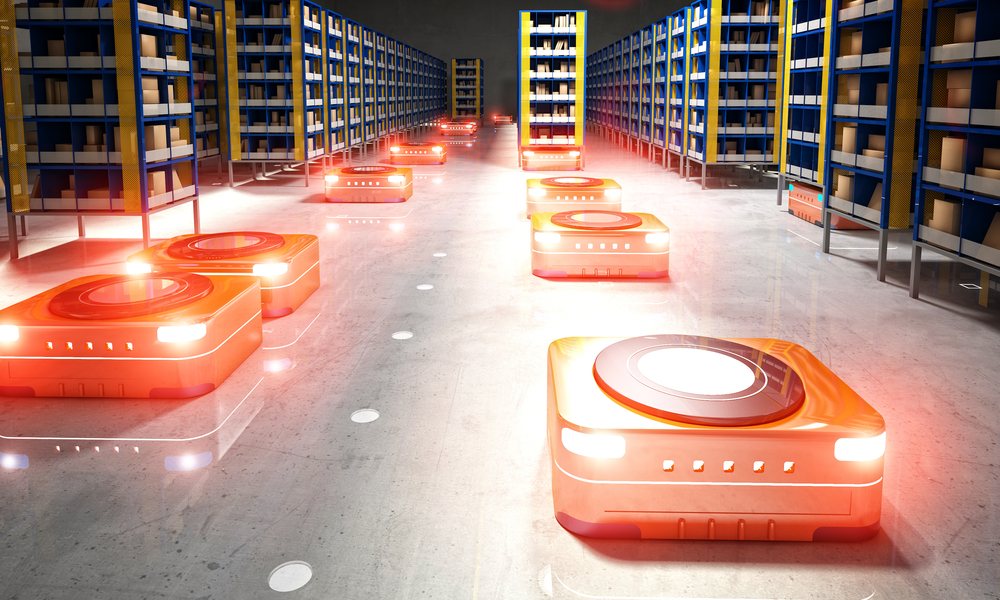
Automating its warehouse is in the mood of time and appears as an almost inevitable progress in the face of the shortage of logistics labor or its aging. In addition, the solutions in the mechanization, robotization and automation market are constantly growing. The offer has diversified and expanded: stacker cranes, sorters, shuttle, mini load, AGV / robots moving in 2 or 3 dimensions, goods to man …. So that the promises to improve the quality of preparation, to accelerate the cadences, to cope with the peaks of activities, to reduce the storage surfaces, the hardness … seem more and more accessible. Is not it time for you to take the plunge? No doubt, but in an enlightened way.
Projects in R.O.I. more than 15 years or even negative
“I have never seen a speaker say that he has completely failed in his automation project …”, recently amused the Director of Operations of a famous group of cosmetics. However, many automation and robotization projects are failures on the economic plan, some having returns on investments (ROI) of more than 15 years, even negative, for not having sufficiently anticipated the constraints and the additional costs induced ( eg maintenance of the installation, loss of flexibility, etc.). On two occasions we have also encountered automatisms that are useless. Here are some points of vigilance to avoid disillusionment.
Attention to the estimation of the performance of the future installation
First, the actual Synthetic Efficiency Ratio (TRS) of an automated installation is often lower than that reported by solution providers, who talk about instantaneous rates rather than averages over time. In real life, your staff will take breaks, first-level maintenance operations, change teams, suffer breakdowns … Thus, it is difficult to accurately estimate the performance of its future automated installation. From experience, we recommend taking TRSs of 60% compared to the instantaneous rates announced by the manufacturers to obtain realistic rates. And for robot-based installations, it is necessary to ask the supplier a minimum commitment rate of the installation, 98% to 99% seeming to us a credible objective.
Attention to the number of positions in goods to man
When one opts for preparations in goods to man (the goods arrive at the preparer, avoiding him to go to pick them), the stations of levy are expensive. We will therefore be tempted to limit the number. However, in peak periods, where we could assign 10 more operators in a conventional manual preparation, goods to man, we will be constrained by the number of sampling stations. This point can be blocking in e-commerce, where the requirement of quality of service is very strong, including during peak periods, as in activities with high seasonality. A solution can then be to play on the working time by passing for example from 2 to 3 teams. But this is not always possible (eg Christmas period, night work, etc.). In fact, the main concern we are seeing is a high rate of search but volume flexibility is also important for the rate of service.
Watch out for WCS
Another point of attention is the automated installation control software: the Warehouse Control System (WCS). Provided by the manufacturer of the automated system, it can turn out to be a black box whose constraints are discovered after the event and not as flexible for use as envisaged during installation. For example, in a goods-to-man order-picking system, we can see that we can not manage apiaries with more than 10 orders, which multiplies the movements of the robots bringing the products. . And it is this constraint that will slow down the installation by becoming its bottleneck. Another example is a packet sorter that requires you to finish a wave before launching a new one: 2 positions are then stuck waiting for the 3rd to complete the task.
A minimum threshold to operate an automated installation
An automated system also impacts the workforce of the warehouse for more than one reason. If it is intended to reduce the movement of operators, it can on the other hand increase their musculoskeletal disorders (MSD) in case of high rates involving too repetitive gestures. It is therefore better to introduce versatility. In the same way, the personnel dedicated to the maintenance of the installation is often more expensive. Finally, a minimum number of qualified people is required to operate the automated installation. We must therefore ensure that they are present in sufficient numbers despite the hazards (eg climate, epidemics, holidays …) and that the capabilities are in line with the level of activity.
Study the order portfolio
An analysis of the order portfolio is essential to know the order structure and the correct automation response. It can also be rich in lessons to know where to put the cursor between the mass flow and the reactivity / flexibility of the installation. For example, a goods-to-man system based on shuttles could be designed to collect from 1 bin to 2 to 4 others, while a system based on shelves driven by robots could bring an apiary of 20 references for break down to 100 orders. Study the rotation of products, their volume and lead times guide in the optimal choice of these solutions.
Consider 3 scenarios
As you will have understood, it is essential to take care of all the constraints likely to limit your flows. Being accompanied to avoid traps can be a great help because it is the experience of multiple projects that makes the difference. We also recommend starting from the existing scenario to consider improvements and encrypt them, before any automation, to measure whether the latter is really relevant. So, is it better to change the information system before automating? It is also important to consider and quantify scenarios upward and downward. What happens if the volumes I estimate fall by 20%? Increase by 30%?
5 keys to success
Let’s summarize in 5 points, to succeed, it is necessary:
1. To consider that one’s activity is unique because to believe that a standard system can cover all cases is illusory;
2. In the face of an unpredictable world, the automated installation must be able to evolve and adapt to its new context within a reasonable budgetary deadline (1 to 2 years maximum);
3. Call on specialists not to get lost in the meandering of the offer of automated solutions that are very different and to consider all their constraints, as well as their interactions;
4. To be accompanied by seasoned consultants who have accompanied multiple projects (and not every 15 years) to maintain objectivity in the face of the seductive speech of the suppliers;
5. Call on the DIAGMA experts who will be happy to guide you!
François Rochet
Partner of DIAGMA
frochet@Diagma.com
Tel: 06 12 45 66 51