They are all intertwined. Logistics is mostly concerned with organizing distribution, shipping and storing and order preparation in an efficient way. Comes from the “maréchal des logis”, a military term coined by Napoleon for his army. Literally it is the person who in the army organizes the “lodging”, a Marshall of Lodgings. As Napoleon once …
Continue reading “What is the difference between supply chain, operations, and logistics?”
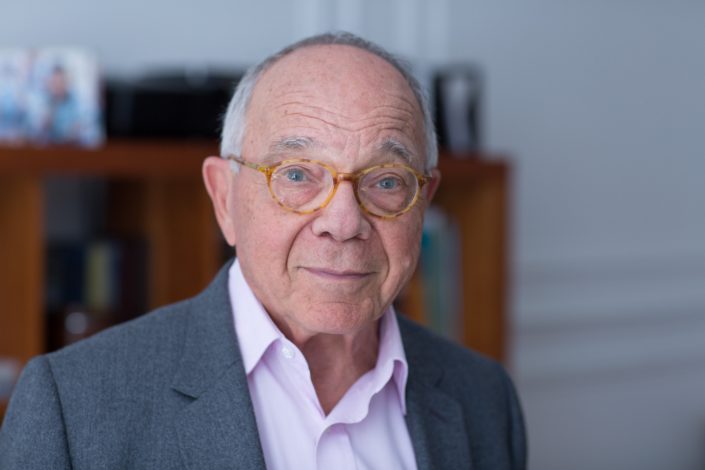
They are all intertwined.
Logistics is mostly concerned with organizing distribution, shipping and storing and order preparation in an efficient way. Comes from the “maréchal des logis”, a military term coined by Napoleon for his army. Literally it is the person who in the army organizes the “lodging”, a Marshall of Lodgings. As Napoleon once said “l’intendance suivra”, meaning don’t bother, “logisticians” will organize food and lodgings behind the stage.
You can also say it meant “don’t bother about supplies, my supply chain managers will take care of everything. They will organize procurement, storage and distribution».
Currently Supply Chain Managers organize the whole supply chain. Together with the Executive Committee they design the Supply Chain and manage it. And the supply chain includes all movements of goods between Company Suppliers and Company Customers, including transformation (production) operations.
But in most cases the Supply Chain Manager will not organize the shop floor in plants nor is he responsible for that. Strangely enough very often he is responsible for logistics operations, organizing the Warehouse and the Shipping. Strangely, because nowadays warehouses are no different from an assembly plant, assembling customer orders. The only reason, I believe, is that warehouses, contrary to factories, are pretty much the same whatever the industry. They stock pallets or cases or individual items, then they prepare customer orders of all sizes and mix.
The Operations Manager is responsible for Operations: the way things are done.
Now in my opinion if you want logic in the system you should have the VP at the top responsible for Operations and Planning. Reporting to him, an Asset Operations Manager responsible for operating the plants and warehouses and the Supply Chain Manager who organizes and plans the movement of goods between all the entities in the network (chain) of supplies.
This means he is responsible for the planning of the movement of goods along the chain. The chain he manages, more of a network in fact, links Company Suppliers to Company Customers. It combines Manufacturing Plants, Distribution Centers and Transportation. This means he contracts with all these entities. He contracts (Service Level Agreement or SLA) with plant and DC managers, specifying for example the rate and cost of output expected from each manufacturing or logistic asset so that he can plan production and distribution,
Together with Purchasing he contracts with Suppliers specifying lead-times and cost per “order quantities”.
And finally, he contracts with Customers, jointly with Sales, again specifying Service to the customer.
The assets can be outsourced of course. In this case the SC manager is a party in choosing and contracting with these outsourced partners.
Let us sum it up:
- At the top, someone (most of the time called an Operations VP), is responsible for delivering efficiently quality products and quality service to customers.
- Reporting to him or her:
- On the one hand Asset Managers (Manufacturing, Warehousing, Transportation), managing daily operations in the plants and warehouses and distribution centers, handling the Physical part of the product. Sometimes Warehousing and Transportation is called Logistics
- On the other a Supply Chain Manager organizing and planning the movement of goods along the Supply Chain, contracting with all parties involved, from Suppliers to Customers. He is responsible for the Service part of the product delivered to the customer.